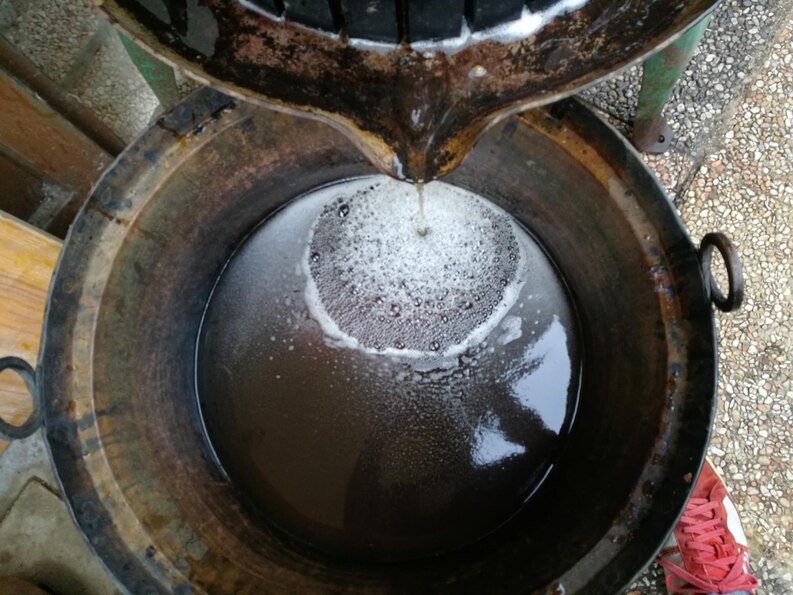
Avoiding issues with industrial grease traps is crucial for businesses in Indiana that handle large quantities of grease. Properly functioning grease traps ensure that operations run smoothly and prevent potential problems that could disrupt daily processes. When grease traps are not maintained, it can lead to severe blockages, resulting in unpleasant odors and costly repairs.
Understanding the early signs of grease trap problems can help facilities act quickly before minor issues become major disruptions. Regular inspections and preventative measures are key components in maintaining efficient wastewater systems. By being proactive, businesses can ensure compliance with environmental standards and avoid penalties related to improper waste management.
By implementing best practices and leveraging modern technologies, facilities can enhance the performance and longevity of their grease traps. This proactive approach not only saves time and money but also promotes a cleaner and healthier environment in and around industrial settings. This blog will explore strategies and tools for avoiding common grease trap issues, making it easier for businesses to focus on their core operations.
Recognizing Early Signs of Grease Trap Problems
Identifying issues with your industrial grease trap early can save you from major headaches down the road. Watch for common indicators like slow drainage, which often signals a blockage. Bad odors emanating from drains or the trap itself suggest built-up grease or food particles. Water backing up from your sinks or floor drains is a clear sign of a problem that needs immediate attention.
Spotting these signs early prevents operational disruptions in your facility. When grease traps malfunction, it can lead to production delays and potential shutdowns to clear the problems, costing time and money. Early detection allows for timely interventions, ensuring that operations continue without a hitch and keeping stress levels low.
Conducting regular inspections is crucial for preventing grease trap issues. Begin by visually inspecting the trap for any clogs or overflow. Check for grease buildup and examine the trap walls and outlet for corrosion or significant wear. Use tools like dipsticks or electronic sensors to measure grease levels accurately. Schedule these inspections weekly or monthly based on your facility's grease output to catch and address problems before they escalate.
Regularly recognizing these signs ensures a seamless operation, cuts down on costly repairs, and helps maintain compliance with environmental regulations. This vigilance keeps your business running smoothly, allowing you to focus on what truly matters.
Preventative Maintenance Practices
Implementing a robust maintenance routine for your grease trap is key to avoiding future problems. Scheduling regular cleanings is vital. This routine prevents grease and solid waste from reaching problematic levels. It also helps extend the life of your equipment by keeping parts free from corrosion and other damage.
Certain tools and techniques enhance the effectiveness of preventative maintenance. Use traps and skimmers to remove surface waste efficiently. A vacuum pump simplifies the extraction of liquid waste from traps. Blades and augers are excellent for breaking up tougher clogs, ensuring a thorough cleansing. These tools contribute to a clean and efficiently running system.
Timely grease trap cleaning greatly impacts your facility’s efficiency. Scheduled maintenance minimizes the risks of unexpected shutdowns due to blockages. It improves the flow of wastewater, enhancing overall system performance. Clean systems also comply with local regulations, avoiding fines and ensuring that your business contributes positively to the environment.
Adhering to these preventative practices ensures that your grease traps work optimally for longer periods. Not only does this save money on repairs, but it also assures the community that the facility values environmental responsibility and smooth, uninterrupted operations.
Enhancing Grease Trap Performance
Improving the performance of an industrial grease trap involves embracing new technologies and practices that can optimize its operation. Advanced cleaning technologies, such as automatic grease removal units and high-efficiency interceptors, play a significant role in maintaining a cleaner system. These tools separate and remove grease automatically, reducing manual labor and the frequency of regular cleanings.
Adjusting business operations to minimize grease input can greatly enhance grease trap performance. Train kitchen staff to scrape excess grease into containers before washing dishes. Implementing procedures for pre-washing can help prevent grease from entering the trap at all. Installing strainers in sinks can catch food particles and solid waste, preventing clogs before they occur.
The use of biological additives is another beneficial strategy. These natural cleaners introduce beneficial bacteria that break down grease, oils, and other organic materials. This process helps maintain trap efficiency and extends the time between necessary deep cleans. By using these natural agents, facilities keep their traps flowing smoothly without relying on harsh chemicals.
By incorporating these strategies, facilities can optimize grease trap performance, reduce operational disruptions, and contribute to a more sustainable approach to waste management. A more efficient system is not only beneficial for the facility but also for the broader community and environment.
Collaborating With Expert Grease Management Providers
Partnering with professional grease management providers offers significant advantages for industrial operations. The right service partner can help ensure that grease traps are maintained effectively, preventing issues before they start. Identify a service provider with expertise in your industry and a track record of reliable service. Look for providers who offer a wide range of services, including regular maintenance, emergency cleanings, and system assessments.
Professional intervention in grease trap maintenance brings expert knowledge and advanced tools that can enhance cleaning outcomes. These experts bring specialized pumps, hydraulic systems, and other equipment that ensure the proper disposal and recycling of grease. Their intervention reduces the workload on internal staff and allows teams to focus on core business operations.
Integrating service packages from professional providers maximizes efficiency across all grease management needs. Bundled services may include grease pick-up, line jetting, and interceptor cleaning. These comprehensive packages offer convenience and ensure that all aspects of grease management are covered, reducing the risk of oversight and maintaining compliance with regulations.
By collaborating with skilled providers, businesses benefit from expert handling of their grease management needs, leading to smoother operations and peace of mind. Choosing the right partner allows facilities to maintain focus on their goals without disruptions.
Discover Grease Trap Solutions from Evergreen Grease
Efficient grease trap management is paramount for the smooth operation of industrial facilities in Indiana. Keeping grease traps in optimal condition requires recognizing early problem signs, establishing routine maintenance practices, and utilizing advanced cleaning techniques. Collaborative efforts with professional grease management providers amplify these practices, ensuring comprehensive grease control that saves both time and resources while contributing to environmental sustainability.
To ensure your facility grips control over its grease management, consider partnering with Evergreen Grease. Our expert team provides tailored solutions to meet your unique needs. Let us handle your grease trap challenges, enabling your team to focus on essential operations without the hassle. Reach out today and discover how Evergreen Grease can enhance your facility’s efficiency and compliance.
Event details
Medium length section heading goes here
Morbi sed imperdiet in ipsum, adipiscing elit dui lectus. Tellus id scelerisque est ultricies ultricies. Duis est sit sed leo nisl, blandit elit sagittis. Quisque tristique consequat quam sed. Nisl at scelerisque amet nulla purus habitasse.
Nunc sed faucibus bibendum feugiat sed interdum. Ipsum egestas condimentum mi massa. In tincidunt pharetra consectetur sed duis facilisis metus. Etiam egestas in nec sed et. Quis lobortis at sit dictum eget nibh tortor commodo cursus.
Odio felis sagittis, morbi feugiat tortor vitae feugiat fusce aliquet. Nam elementum urna nisi aliquet erat dolor enim. Ornare id morbi eget ipsum. Aliquam senectus neque ut id eget consectetur dictum. Donec posuere pharetra odio consequat scelerisque et, nunc tortor. Nulla adipiscing erat a erat. Condimentum lorem posuere gravida enim posuere cursus diam.